Desde hace unos años, la impresión 3D está presente en muchos ámbitos de la producción. Factores como la eficiencia en el proceso de fabricación, su rápido desarrollo y especialmente la libertad casi absoluta para crear formas y diseños, suponen una gran ventaja frente a otros procesos productivos.
En el mundo del motor su uso no está tan extendido, pero cada vez son más los fabricantes que se aventuran con esta tecnología. Porsche es una de ellas, y acaba de presentar un programa sobre los usos que planea llevar a cabo durante los próximos años: piezas para el motor, piezas para algunos elementos del habitáculo (estructuras de asientos, principalmente) y piezas de recambio para vehículos clásicos.
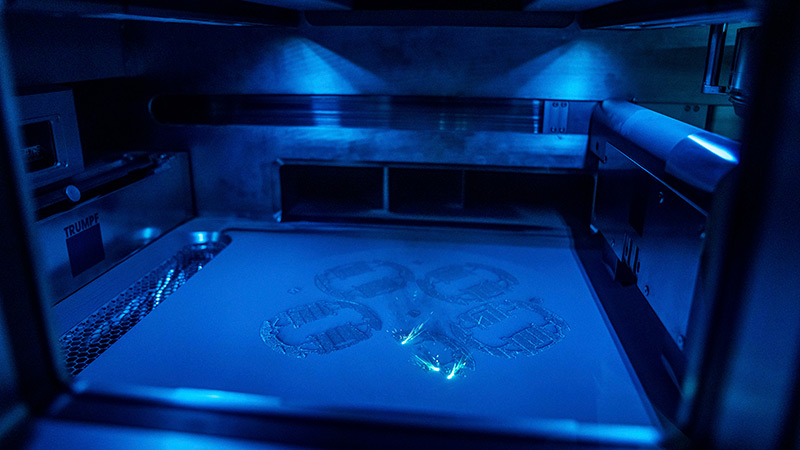
Pistones
Uno de los desarrollos en los que más recursos está inviertiendo y con el que más beneficios espera conseguir (tanto de rendimiento como económicos), es la impresión de pistones en 3D. Ya han llevado a cabo pruebas con resultados positivos en el motor del 911 GT2 RS, uno de los modelos más potentes de su gama (ficha técnica). Según Porsche, los pistones impresos en 3D que han probado en este vehículo tienen una estructura optimizada para integrar un conducto de enfriamiento anular detrás de los segmentos y además pesan un 10 % menos (cada uno de ellos) que los convencionales forjados del modelo de producción. Con ello, la temperatura de los pistones es menor (hasta 20 grados menos en el área de los segmentos), la velocidad de giro del motor es superior (unas 300 rpm más) y el rendimiento general es más elevado (Porsche lo cifra en unos 30 CV adicionales; 730 CV en total).
El material con el que fabrican estos pistones es un polvo soldable a partir de una aleación de aluminio patentada por Mahle (M174+). Según los responsables del desarrollo, los valores característicos del material impreso son comparables con los del material fundido para pistones de producción. Para evaluar la idoneidad del polvo para el proceso de fabricación, se han llevado a cabo múltiples pruebas de calidad en cooperación con la compañía óptica Zeiss, como la inspección por microscopio óptico, microscopio electrónico de barrido y microscopio de rayos X.
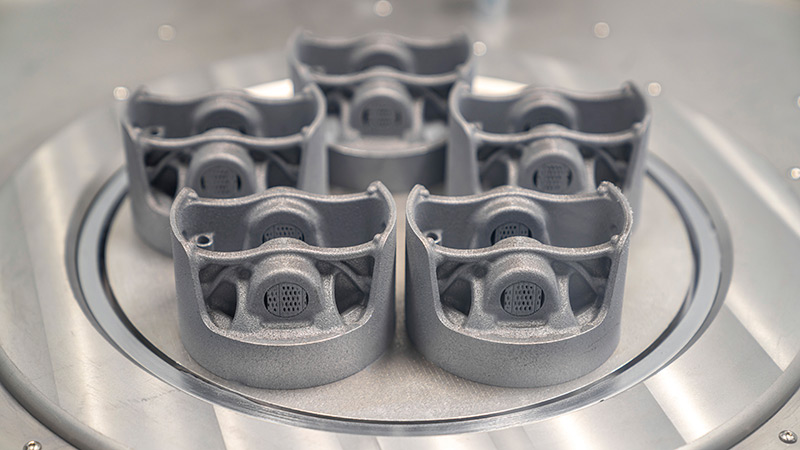
La empresa de tecnología Trumpf ha sido la responsable del desarrollo del proceso de producción y la impresión. Con las máquinas TruPrint 3000, sueldan el polvo capa por capa utilizando el proceso de fusión de metal con láser (LMF, por sus siglas en inglés), también conocido como fusión de lecho de polvo con láser (LPBF, también por sus siglas en inglés). En este proceso, el rayo láser fusiona el polvo con un grosor en el rango de µm (0,02-0,1 milímetros), formando así el pistón capa por capa. Las piezas del pistón se producen de esta manera con aproximadamente 1200 capas, proceso para el que se necesitan unas 12 horas.
Para comprobar el rendimiento y la resistencia de los pistones, se instalaron seis de ellos en el motor de un 911 GT2 RS y se realizaron pruebas en un banco de rodillos durante 200 horas. En dichas pruebas se simularon las condiciones de una conducción exigente en circuito (con aproximadamente 6000 kilómetros recorridos a una velocidad media de 250 km/h), a plena carga y a diferentes rangos de revoluciones. Según Porsche y sus socios colaboradores en el desarrollo del proyecto, los resultados fueron muy buenos.
Asientos baquet
Otro de los ámbitos que Porsche está explorando con esta técnica es la fabricación de estructuras de asientos de tipo baquet. La sección central de las unidades que ha producido hasta la fecha (por el momento como versiones pre producción) está fabricada con impresión en 3D y con tres niveles de firmeza: duro, medio y blando. Con este producto, Porsche dice que el ajuste al cuerpo es mucho mejor, similar al de los asientos utilizados en modelos de competición, el peso es menor y el diseño puede ser personalizado.
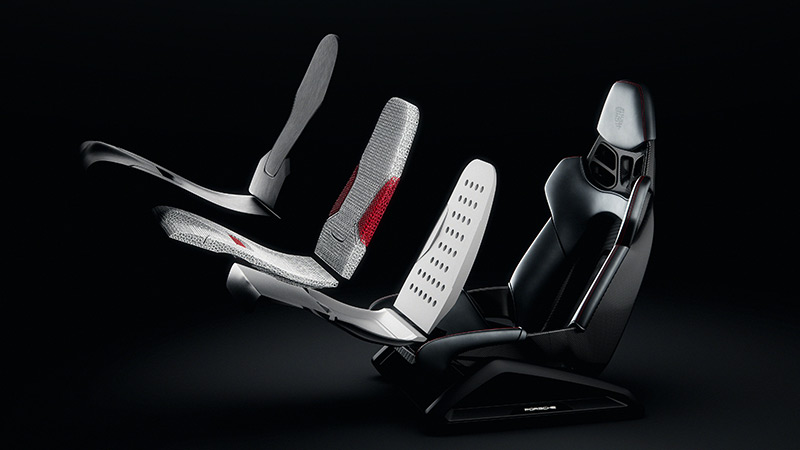
La construccción de la sección central es de tipo sándwich, es decir, un soporte base hecho de polipropileno expandido (EPP por sus siglas en inglés) está unido a una capa de confort transpirable que consiste en una mezcla de materiales a base de poliuretano fabricados con una impresora 3D. La piel exterior del asiento está hecha de «Racetex» y presenta un patrón específico para que transpiren mejor.
Tras un periodo de pruebas en circuitos que ya se está llevando a cabo, Porsche ofrecerá este tipo de asientos en las gamas 911 y 718 para mediados de 2021. Además de una amplia gama de colores, también se desarrollarán y ofrecerán asientos adaptados al contorno corporal específico del cliente.
Piezas para vehículos clásicos
Uno de los problemas más recurrentes a los que se enfrentan los propietarios de coches clásicos es la falta de repuestos, más aún cuando se trata de de vehículos poco convencionales o de fabricación muy limitada. Con la fabricación de piezas en 3D, Porsche dice que dicho problema quedará resuelto en un corto plazo de tiempo.
Ya ha iniciado la fabricación de algunas piezas de esta manera, como por ejemplo la palanca de liberación del embrague del 959, un vehículo del que solo se fabricaron 292 unidades. La pieza original, fabricada en hierro fundido, tiene una demanda muy baja y resulta mucho más sencillo, barato y eficiente producirla con una impresora 3D que con los útiles de la época (que requieren muchos más recursos). Para el proceso de fabricación se aplica una capa de acero para herramientas en polvo de menos de 0,1 milímetros de espesor en una placa de procesamiento. En una atmósfera inerte, un haz de luz de alta energía derrite el polvo en los lugares deseados para crear una capa de acero. Por lo tanto, se produce el componente tridimensional completo capa por capa. Una vez completado el proceso y para probar su rigidez y funcionamiento, se lleva a cabo una prueba de presión con una carga de casi tres toneladas y un examen tomográfico de fallos estructurales. Además, también se realiza una prueba dinámica en un vehículo para comprobar su funcionamiento en condiciones de circulación reales.
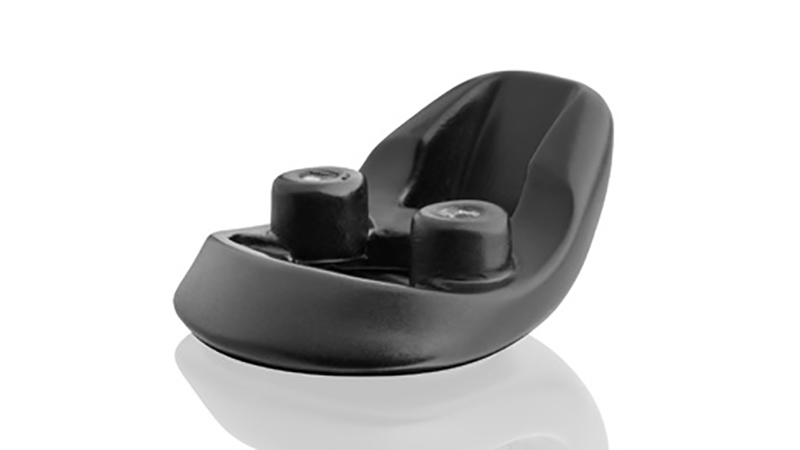
Actualmente, Porsche está fabricando otras ocho partes utilizando impresión 3D, como por ejemplo la base del retrovisor interior del 911 Speedster, un soporte del sistema de escape de los 356 B y 356 C o la junta de la toma de combustible del 959. Las piezas en cuestión son piezas de acero producidas mediante el proceso selectivo de fusión por láser, y componentes de plástico fabricados con una impresora SLS (sinterización selectiva por láser; es un proceso en el que el material se calienta en una cuba hasta justo por debajo del punto de fusión. Posteriormente, un láser de alta potencia fusiona el polvo de plástico en el punto correcto causando que las partículas se solidifiquen). Según Porsche, todas las piezas están sujetas, como mínimo, a los requisitos de calidad del período de producción original, aunque generalmente cumplen con estándares más altos.
Porsche, a través de su división de vehículos clásicos «Porsche Classic», está probando actualmente si la impresión 3D es adecuada para la producción de otros 20 componentes más.
«Según Porsche, los pistones impresos en 3D que han probado en este vehículo tienen una estructura optimizada para integrar un conducto de enfriamiento anular detrás de los segmentos y además pesan un 10 % menos (cada uno de ellos) que los convencionales forjados del modelo de producción.»
Puesto que todos los pistones del mismo motor deben pesar exactamente igual (con una tolerancia mínima), si uno de ellos pasa a pesar un 10% menos que antes, todos lo harán en la misma medida. Pero además si se dice que pesan un 10% menos, lógicamente el conjunto también pesará un 10% menos.
Tampoco es tan novedoso, hace tiempo que BMW fabrica los bloques de algunos de sus motores por impresión 3D, creo que empezaron en una de sus factorías de asía.
Es más, creo incluso que fueron ellos los pioneros en empezar a retirar moldes de piezas de recambio al pasar a producirlas por impresión 3D tras digitalizar poco a poco la base de datos de repuestos.
Una gran ventaja para la producción de repuestos para vehículos clásicos ya de paso
(Perdón por poner este comentario aqui, ya se que no corresponde, pero no sabía donde ponerlo)
Una sugerencia a Km77.com. Veo que en general el nivel de discusión en las entradas del blog es bastante interesante. Echo de menos poder comentar también los artículos de km77.com, no sólo los del blog. Por ejemplo en las pruebas de coches. ¿No sería posible activar los comentarios también en ellas?
Excelente artículo y un blog fantástico.